Stromspeicher für die Elektromobilität bestehen aus beschichteten Metallfolien, die in regelmäßigem Wechsel aus Anode, Trennfolie und Kathode übereinandergelegt und zu Paketen verbunden werden. Hierbei ist höchste Genauigkeit erforderlich, denn schon kleinste Beschichtungsfehler oder Positionsabweichungen der beschichteten Bereiche auf den Folien können die Qualität der Batterie beeinträchtigen. Für die vollautomatisierte Qualitätskontrolle mithilfe computergestützter Bildanalyseverfahren kommen wegen der hohen Anforderungen an Auflösung und Arbeitsge-schwindigkeit Contact-Image-(CIS)-Sensoren zum Einsatz.

„Die von WHEC entwickelten Contact-Image-Sensoren stammen ursprünglich aus den Fotokopierern – nichts Besonderes jedoch clever industrialisiert“, weiß Stefan Basig, Leiter Vertrieb und Marketing beim Machine Vision Systemintegrator Compar AG in Pfäffikon SZ.
Diese Sensormodule liefern dank einem effizienten Linsensystem ein realitätsnahes, verzerrungsfreies 1:1-Bild des gescannten Objekts. Weiterer Vorteil ist ihre kurze Brennweite, so dass sie ohne die z.B. bei Kopierern verwendeten Glasscheiben sehr dicht an der zu untersuchenden Oberfläche eingesetzt werden können. Diese kurze Entfernung zum Prüfling hat den doppelten Nutzen, dass die Lichtverluste im Spalt zwischen Sensor und Objekt deutlich geringer sind und zugleich die Empfindlichkeit gegenüber Streulicht herabgesetzt wird.
Jedoch Hauptaugenmerk und wichtigster Vorteil gilt der verzerrungsfreien Bildgenerierung mit bis zu einer Abtastbreite von 2 Metern. Weiter weisen die Sensoren dank der kleineren Linsen geringere Abmessungen und Gewichte auf. Dies alles ermöglicht kompakte Abmessungen. CIS-Sensoren können daher meist problemlos im gewünschten Umfeld platziert werden.
Zahlreiche Varianten für unterschiedlichste Einsatzbereiche
„Dank ihrer Vorteile konnten CIS-Sensoren im Bereich der Oberflächeninspektion bereits eine ganze Reihe von Einsatzgebieten erobern“, ergänzt S. Basig. Dazu gehören Prüfaufgaben bei allen möglichen Arten von Oberflächenbeschichtungen, bei Textilien, bei Folien und Druckerzeugnissen, aber auch bei der Prüfung von Banknoten und Medizintechnik-Produkten, in der Halbleiterherstellung oder bei verschiedensten Anwendungen im Maschinenbau. Die Entwicklung anwendungsspezifischer Ausführungen führte nach und nach zu immer mehr Varianten.
CIS-Sensoren gibt es heute in Breiten von 18 bis 1960 mm, für unterschiedlichste Lichtwellenlängen von monochrom über RGB-Farbe bis zu Infrarot oder Ultraviolett sowie mit oder ohne integrierte Lichtquelle. Es gibt Ausführungen für besonders hohe Auflösungen von bis zu 1200 Bildpunkten pro Zoll (DPI, Dots Per Inch) sowie für Scangeschwindigkeiten von bis zu 2,46 m/s (monochrom) bzw. 0,82 m/s (Farbe). Als aktiver Entwickler ist der Hersteller bereit, für neue Einsatzbereiche weitere spezifisch angepasste Varianten zu entwickeln.

Herstellung von Folien für Kfz-Batteriezellen

„Bei den Kfz-Herstellern steht heute die Entwicklung hochwertiger Akkumulatorsysteme weit oben auf der Prioritätenliste“, verrät S. Basig. Eine Schlüsselrolle kommt hierbei der Herstellung der beschichteten Metallfolien zu, welche in den Batterien als Pole dienen. Diese Folien bestehen aus Metallbändern (Aluminium für die Kathode, Kupfer für die Anode), die mit dünnen Lagen aus Graphit beziehungsweise aus einem Gemisch von Metalloxiden beschichtet sind. Der eigentliche Akkumulator entsteht aus übereinander geschichteten Lagen von Anoden und Kathoden, die jeweils durch Separatorfolien getrennt sind. Diese sind für die Lithium-Ionen in der Elektrolytflüssigkeit durchlässig. Sie wandern als Positives Ion daher beim Laden zur Kathode. Beim Entladen gehen die Li-Ionen wieder durch die Folien zurück, während die an der Kathode freigesetzten Elektronen das Fahrzeug antreiben und so zur Anode zurückkehren.
CIS-Einsatz im Bereich der Batteriefolieninspektion
„Entscheidend für die Leistungsfähigkeit und Wirkungsgrad der Batterie ist die Qualität der Beschichtung, die beidseitig sowohl auf der Vorder- als auch auf der Rückseite der Elektroden aufgebracht wird“, weiß S. Basig. Deshalb muss der Beschichtungsprozess kontinuierlich vollautomatisch überwacht werden. Diese Kontrolle erfolgt nach dem Aufbringen, Trocknen und Walzkompaktieren der Beschichtung.
Hierbei kommen beidseitig monochrome CIS-Sensoren in Kombination mit externen Lichtquellen (HLU) zum Einsatz. Zu kontrollieren ist neben der Vollständigkeit der Schicht auch, dass diese weder Fremdkörper noch Kratzer aufweist. Auch muss sichergestellt werden, dass die Beschichtung nur innerhalb der vorgesehenen Bereiche erfolgte und dass sie auf beiden Seiten des Bandes deckungsgleich aufgebracht wurde. Und last but not least ist ebenfalls zu prüfen, dass beim Teilen des Bandes die vorgegebenen Dimensionen eingehalten werden.

Vollständige Integration in die Compar-Software VISIONexpert®
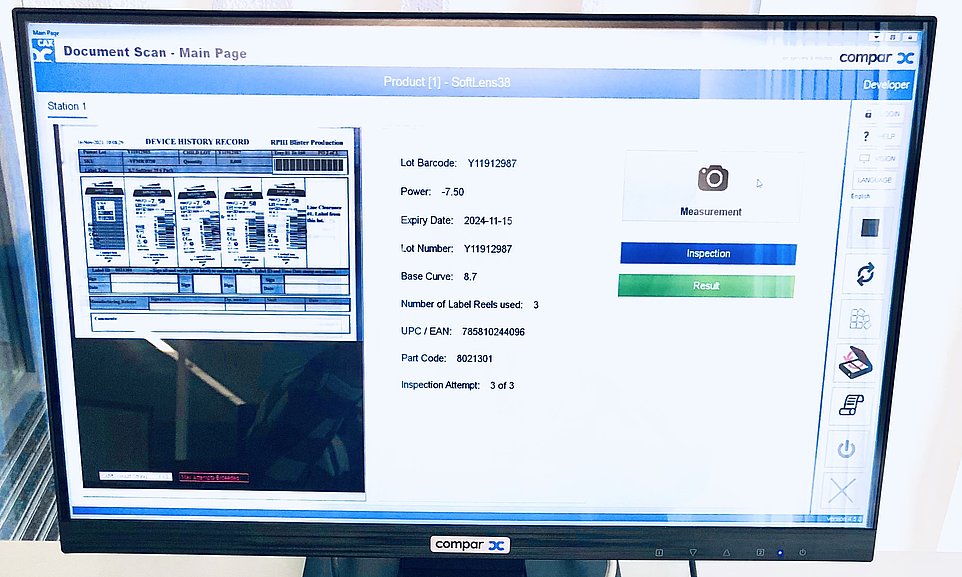
„Die CIS-Sensoren haben uns mit ihrer Leistungsfähigkeit überzeugt, so dass wir die entsprechenden Anpassungen und Treiber bereits vollständig in unsere wichtigste Software VISIONexpert® integriert haben“, bekräftigt S. Basig. Diese innovative Bildverarbeitungssoftware mit vielen Freiheitsgraden und Funktionen ermöglicht die Erstellung bzw. Konfiguration von robusten Lösungen für alle möglichen visuellen Inspektions- und Prüfaufgaben im Bereich Automation und Prozesskontrolle. Sie ist zentraler Baustein für die zahlreichen Lösungen, die Compar bei Qualitätssicherungslösungen für eine Vielzahl unterschiedlichster industrieller Anwendungen entwickelt hat.
Erfreulich ist in diesem Bereich die Innovationsfreude des CIS-Herstellers WHEC. In Zusammenarbeit mit Compar wäre so zum Beispiel die Entwicklung von speziell an die Anforderungen des Kunden angepasster CIS-Sensoren denkbar.