Rundlaufmessung von Wellen
Die Firma Sirona in Bensheim (D) stellt Schleifanlagen her, mit denen Zahnfüllungen automatisch ab CAD – Daten hergestellt werden. Die Anforderungen an die Genauigkeit der Füllungen sind hoch, entsprechend genau müssen auch die Geräte arbeiten. Die bei der Herstellung verwendeten Schleifer sind zwar Verbrauchsmaterial, müssen jedoch sehr präzise sein und ihr Rundlauf muss im Mikrometerbereich liegen. Mit Hilfe der industriellen Bildverarbeitung können die Produkte im Herstellprozess mit hoher Präzision zu 100% geprüft werden.
Definition des Rundlaufs
Als Rundlauf wird der maximale Abstand der Kurve bezeichnet, den die Spitze der Welle oder des Schleifers bei einer Drehung um 360° zum Zentrum dieser Achse beschreibt. Die Richtung der Drehachse wird dabei durch die Achse des Schafts bestimmt.
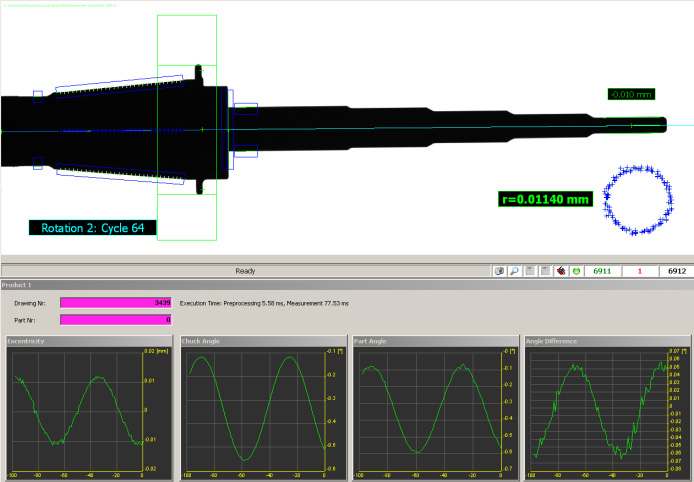

Messung des Rundlaufs
Für die Messung des Rundlaufs wird der Schleifer in eine Spannzange eingespannt und rotiert.
Das Bildverarbeitungssystem nimmt während einer Umdrehung des Schleifers 64 Bilder auf und bestimmt in jedem Bild Drehachse und Lage der Spitze.
Für die Bildaufnahme werden eine Kamera mit 2456 Pixel x 2058 Pixel, eine telezentrische Optik und eine kollimierte Beleuchtung verwendet.
Abb.2 zeigt im oberen Bereich eine Bildaufnahme und darunter den Messverlauf der Drehachse, der Position der Spitze sowie die Messungen für den Rundlauf von Achse und Spitze.
Im oberen Bereich ist ebenfalls das Ergebnis der Rundlaufmessung nach DIN EN ISO 1101 eingeblendet, hier mit einem Radius von 11.4 Mikrometern.
Projektablauf
In einer ersten Phase wurden Vorversuche zur Überprüfung des Messkonzeptes durchgeführt. Dank der PC-basierten Bildverarbeitungsplatt-form VISIONexpert® war ein rasches Prototyping möglich. Es handelt sich bei dieser Plattform um ein PC-basiertes System mit hoch entwickelten Algorithmen für die dimensionelle Messtechnik.
Die Messungen wurden an Musterteilen überprüft und statistisch ausgewertet. Der Vergleich der Messungen des Bildverarbeitungssystems mit denjenigen eines Koordinatenmesssystems zeigte eine sehr hohe Übereinstimmung der Werte (Abb.3). Da bei den Versuchen alle mit dem Bildverarbeitungssystem aufgenommenen Bilder automatisch gespeichert wurden, konnten einzelne Ausreisser wie zum Beispiel Teil 2 in Abb.3 näher analysiert werden. Dabei stellte sich heraus, dass die Abweichungen auf Schmutzpartikel zurückzuführen waren, was wiederum einen nützlichen Hinweis bezüglich Sauberkeitsanforderungen für die Realisierung gab.
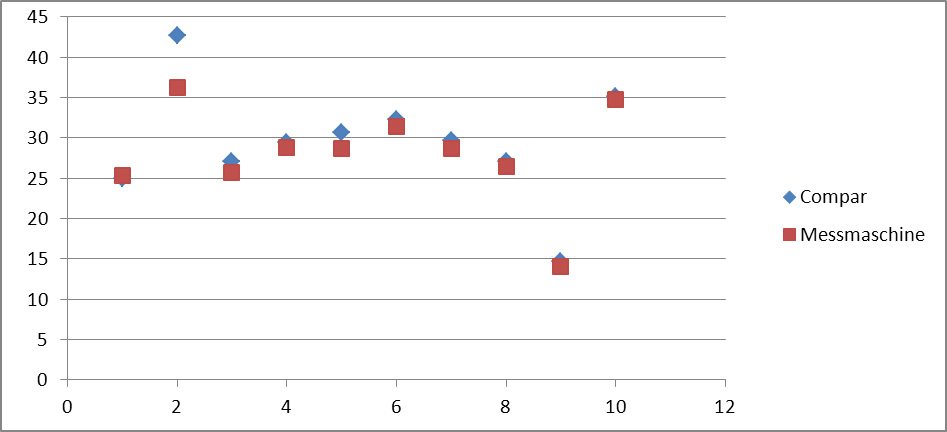

Realisierung
Die Realisierung erfolgte auf derselben Plattform auf der das "Fast Prototyping" gemacht wurde. Sie ging zügig vonstatten, da VISIONexpert® gleichzeitig auch das Zielsystem war.
Für die Automatisierung wurde eine automatische Beschickung der Prüfstation gebaut, die von einem spezialisierten Anlagenbauer unter Verwendung eines EPSON-Roboters realisiert wurde. Abb.4 zeigt einen Teil der Messanlage.
Fazit
Die Vorteile der vorgestellten Lösung sind überzeugend:
- Die Messgenauigkeit des Bildverarbeitungssystems ist vergleichbar mit derjenigen des früher eingesetzten Koordinatenmesssystems.
- Dank der Automatisierung konnte die Gesamtzykluszeitzeit von ca. 3 Minuten pro Teil auf 18 Sekunden reduziert werden. Dank der kurzen Zykluszeit kann nun auch bei grösseren Stückzahlen eine 100% inline Prüfung durchgeführt werden.
- Bei den Kosten des Prüfsystems konnten massive Einsparungen erzielt werden, da die Bildverarbeitungslösung um mehr als einen Faktor 6 günstiger ist als eine Messmaschine auf Basis eines Koordinatenmesssystems.
- Schlechtteile werden frühzeitig erkannt und vor einer weiteren Verarbeitung ausgeschieden, was wiederum Kosten spart.
- Die gemessenen Daten können zusammen mit den Prüfbedingungen automatisch protokolliert werden. Qualitätsnachweis und Rückverfolgbarkeit sind damit sichergestellt.
Dank der Automatisierung kann die Produktivität nun mit dem steigenden Produktionsvolumen Schritt halten und die Firma Sirona Dental Systems kann so ihre Stellung als weltweit führender Hersteller von Anlagen und Geräten für den Dentalbereich festigen.