When it comes to the transition from combustion engines to electric drives, the automotive industry is expecting phenomenal growth in the coming decades. The key to this is the ongoing development of batteries, the performance and costs of which do not yet meet customer expectations. To this end, manufacturers need pilot plants that allow for testing various coatings and processing technologies under production-based conditions. Below you find an interview with a Swiss engineering company that is a global player in this field.
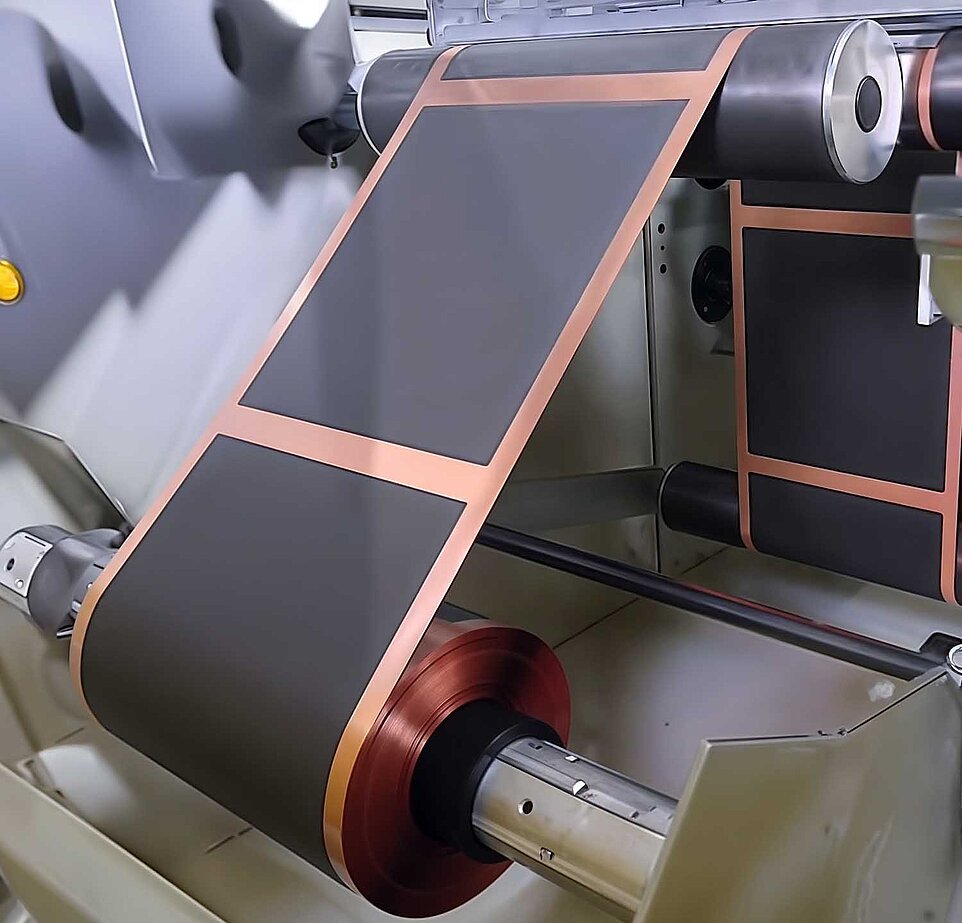
“Starting as a manufacturer of textile dyeing systems, we have become a global engineering partner for sophisticated coating technologies,” says Clemens Disch, Sales & Marketing Manager for Mathis AG in Oberhasli (Switzerland). With currently around 60 employees, the family-run company develops and implements state-of-the-art coating systems for high-tech industries such as the automotive sector, the chemical industry, producers of lithium-ion batteries and solar cell manufacturers. Being partners to their customers, the Mathis specialists help to realise actually functioning system technologies for new ideas and technological approaches. These pilot systems enable customers to test the practical viability of new approaches. The feasibility of the system concept can thus be thoroughly verified. This serves to ensure that the large-scale systems built later at high capital expenditure also deliver the intended result. For such projects, Mathis relies on a dense network of proven local supply and development partners.
Lithium batteries for the automotive sector
“Even though their design principle has been known for some time, lithium-ion batteries for road traffic are still one of the hottest development subjects for automotive manufacturers,” Nico Brand from the Technical Engineering Department adds. The currently available solutions’ road capability in terms of range, charging speed, cycle stability and costs cannot convince many customers. In order to make progress, numerous possible variants would have to be analysed and optimised. In principle, suchlike accumulators are made up of cells, each consisting of an anode and a cathode with a separator membrane in between. The anode is a copper foil covered with an anode mass containing graphite. The cathode is made of aluminium with a coating that contains ions of transition metals such as cobalt, nickel, manganese or iron. The separator membrane is permeable to the lithium ions of the electrolyte and thus allows for charge transport. The coatings are applied as a paste-like mass in one or more layers simultaneously or one by one. Some of them contain solvents that are highly harmful to health and require complex drying and cleaning processes for the exhaust air. The coating is applied using various methods such as slot nozzles or doctor blades in thicknesses between 10 and 350 µm. In order to produce efficiently, the industry often processes the widest possible strips, onto which separate bars are then applied. Sometimes the strips are also cut in order to create individual “patches”. Depending on the respective system, the coating is initially applied to just one side or to the top and bottom at the same time. In systems that process one side only, the strip will subsequently be coated on the opposite side in a second run. For the production of the actual accumulators, the finished strips are divided into pieces that fit together, whereby there must be no displacement between the top and bottom.
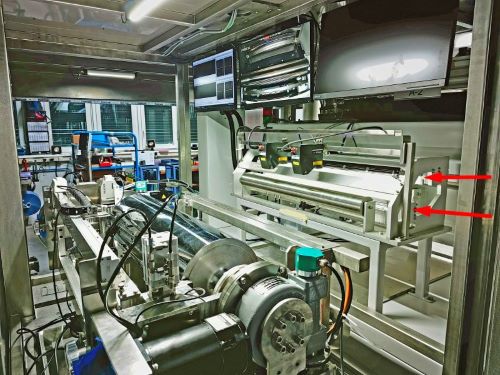
Fast CIS special sensors for position control
“One of the key points in making suchlike coating systems is therefore reliably observing the tight position tolerances between the layers on the top and bottom side of the foils,” explains Clemens Disch. As reference always serves the strip’s edge on the right in the direction of travel. In relation to this, the coating must maintain a defined distance with a position tolerance of ± 0.2 mm. The CCD camera systems used so far were not reliable; the current width of 760 mm already required the use of several parallel cameras. Instead, it was decided to use a so-called contact image sensor (CIS). These are “line scan cameras” like those used in copy systems. However, much higher levels of accuracy and speed are required for coating. The CIS sensor now used is 800 mm wide and consists of almost 19,000 monochrome photocells with fixed focus optics set up as linear array. The distance in between the individual photocells is 0.042 mm. Two rows of light-emitting diodes are also integrated, one in front of and one behind the photocell array. A significant difference to the simple CIS sensors in copiers is the scanning speed, because the strip, which runs through at up to 10 m/min, is to be recorded at a scanning rate of almost four MHz.
Another important aspect for selecting the sensor is its ability to cope with extremely tricky contrasts that range from shiny metallic and reflective to matte black and absorbent. In this case, additional equipment with an obliquely arranged light bar was thus required. Two such systems are used per plant, one on the top and one on the bottom side of the strip. The upper sensor identifies both the strip edge position and the width of the coating(s), while the lower sensor only monitors the strip position.
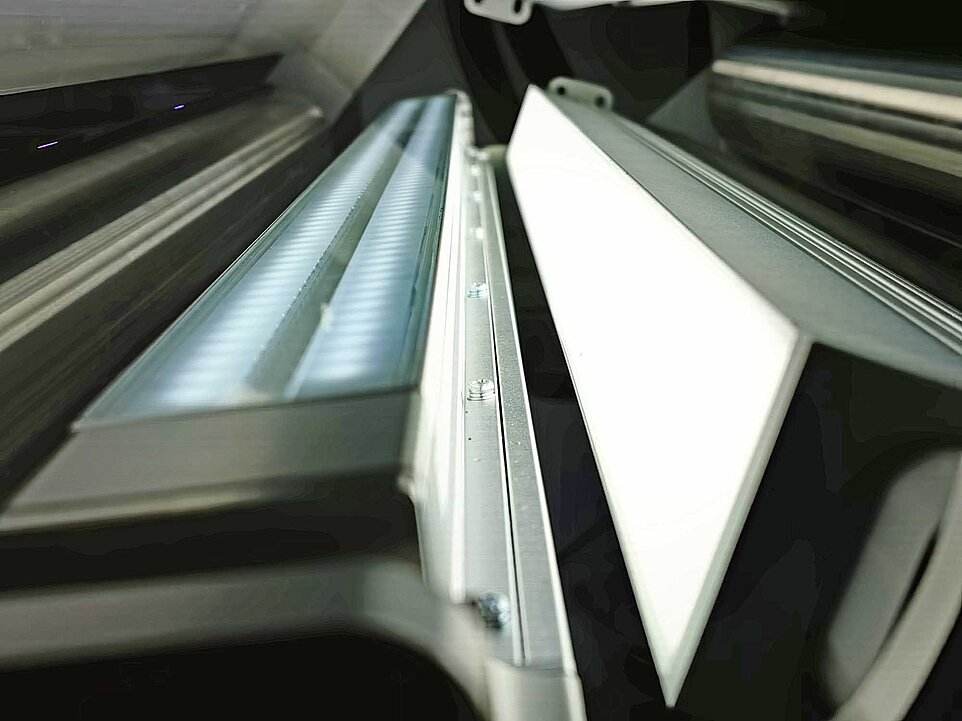
Swiss support for a high-tech sensor from the Far East

“A suitable sensor can be found in a Chinese manufacturer’s product range,” N. Brand recalls. The decisive prerequisite for this choice – apart from the fact that the required hardware properties were being met – was the extensive engineering support provided by the responsible Swiss representative, Compar AG located in nearby Freienbach. Compar, a system integrator for machine vision and robotics with decades of experience, has developed a software platform named VISIONEXPERT for this purpose. VISIONEXPERT is an extremely flexible tool that helps to solve a wide variety of tasks in the field of image capturing and optical defect detection. Thanks to its ease of use and numerous interfaces, it is ideally suited for the efficient development of customer-specific solutions.
After making contact in mid-2022, a first order was placed in August. This was followed by a development collaboration lasting several months, which met the expectations of both parties. Compar set up the CIS sensors for the task so that later calibration was not needed. In addition, the software required for the optimal setting of the lighting, image evaluation and conversion into control signals for correcting the strip position on the rollers was implemented.
Mathis was able to obtain a first order for a pilot coating system equipped with a CIS sensor in January 2023, and the internal acceptance of the functionally assembled line took place in May 2023. In December 2023, the customer’s approval was given after the Factory Acceptance Test (FAT) had been passed successfully. Since it was first installed, the CIS sensor has been working without any problems. Mathis is now equipping a second line with this sensor technology, and four more projects are already in the pipeline.
Excellent collaboration
“Compar holds decades of experience in developing camera-based systems for automation and quality control and has proven to be a competent and responsive partner,” says Clemens Disch. Upon being delivered, the CIS system first remained with Compar for two months in order to work out the ideal setting for different foils and coating variants. In particularly this also applied to the lighting, for which an additional inclined light bar was installed. The system was then mounted to the pilot system. At that point, Mathis’ software department took over with integrating the signals coming from the CIS control into the PLC of the conveyor system. Right from the start, the collaboration was a full success. Compar has proven to be a development partner on par, always responding quickly to any questions or problems that might arise. Even after the system had been integrated with the conveyor system, Compar employees were often on site in less than an hour, if so required. Good experiences have also been had with online support and cooperation via telephone. Compar has proven to be a supply partner with whom they would be happy to tackle more projects in the future, says C. Disch.
Klaus Vollrath b2dcomm.ch
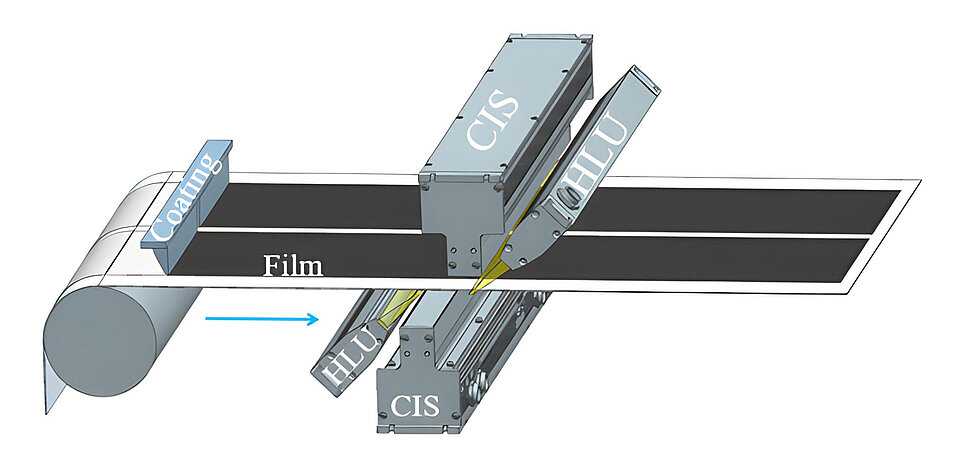